什么是 DMAIC?
商界中有很多行话,我们听到也不会给予太多关注。“DMAIC"(发音为 “duh-may-ik”)就是一个典型示例。简而言之,该首字母缩略词代表 “定义、测量、分析、改进和控制”,是一种以数据为导向解决问题的方法,涉及对产品、设计和流程的逐步完善和优化。
摩托罗拉工程师 Bill Smith 在 20 世纪 80 年代提出了 DMAIC,作为六西格玛方法的一部分,该方法依靠测量和分析来尽可能提高运营效率。其目标是什么?改进流程。
DMAIC 流程有哪些不同步骤?
Smith 设计了 DMAIC 的五个相互关联的步骤,以产生累积效应:基于先前阶段中生成的信息和数据,并对您的发现进行迭代。(专家提示:我们的许多客户都喜欢通过 DocSend 收集的实时分析!)
定义:
定义阶段确定遇到了哪些问题以及解决该问题需要采取哪些措施。听起来很容易理解,但流程的这一部分却至关重要,该流程陈述了实现目标所必需的问题、目标和范围。通过定义,您会了解到哪些元素属于关键质量特性,即 “CTQ”。团队主管和项目经理通常为其团队或项目许可证文件制定 SIPOC(供应商;输入;流程;输出;客户)示意图。
测量:
明白问题了吗?太棒了;让我们概述一下您将如何测量和观察您对其所做的更改。测量阶段的目的是确定您现有的流程性能并确定要分析哪些数据。(在此基础上,您可以使用数据收集计划在进行更改时监控性能,并在项目结束时进行比较。)
请从以下方面进行分析:
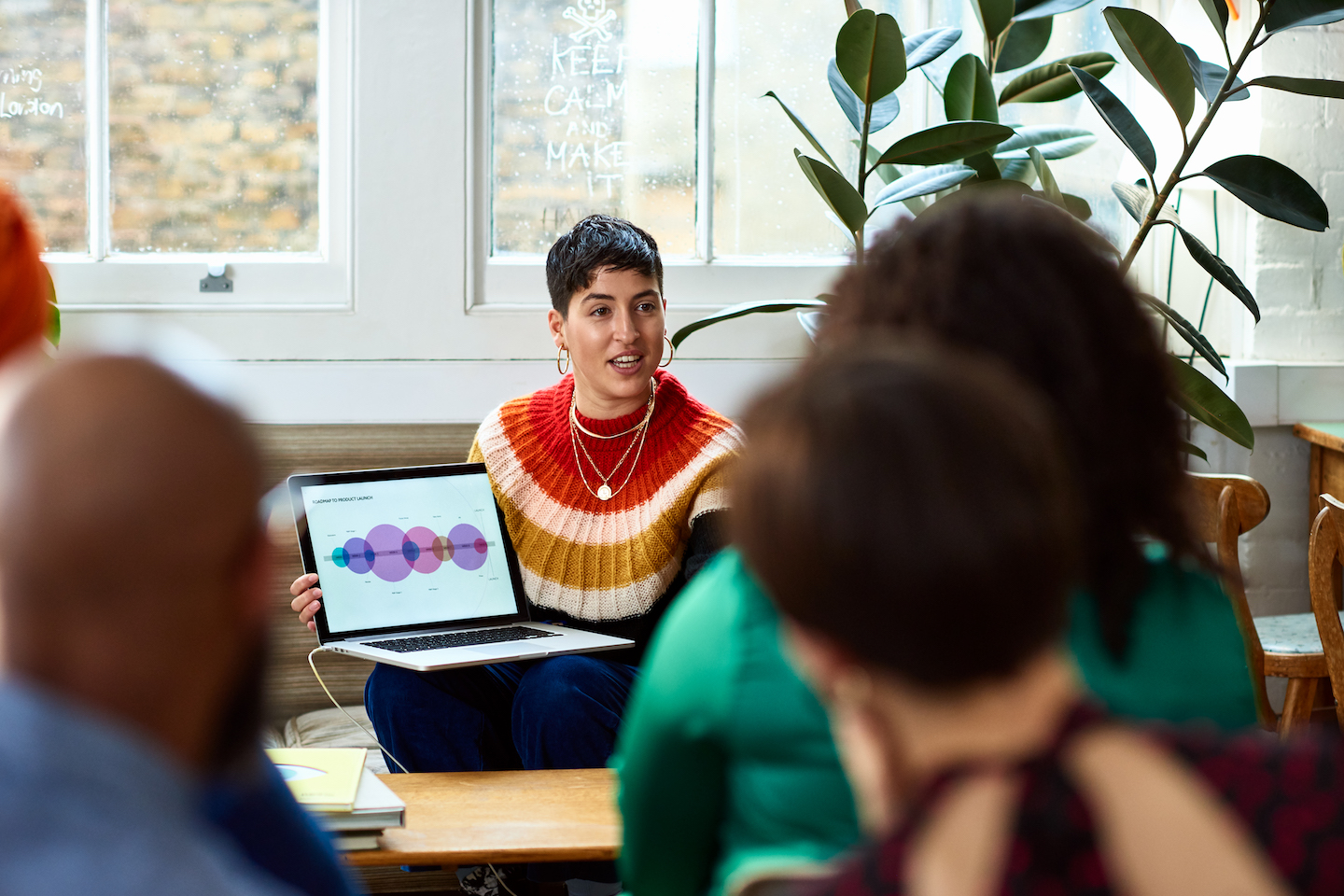
现在,您应该建立了数据基线,可以用来开始制定与流程相关的决策。恭喜!欢迎来到分析阶段,此时您将研究这些数据。您和您的团队成员将使用您掌握的数据绘制当前流程图,以此了解现有流程中的问题是从哪里开始的。(也无需使用复杂的六西格玛工具;使用鱼骨图和帕累托图就足够了,这些图是进行根本原因分析的常用方法。)确定了几个根本原因后,就让您的团队参与进来,以帮助确定未来 DMAIC 流程的重点。
改进:
是时候开始对流程进行实际改进了。在改进阶段,与您的团队合作,寻找可实施和测量的创造性解决方案。集思广益和召开有效的会议至关重要。想出解决方案之后,您需要测试、验证并实施解决方案。计划-执行-检查-行动即“PDCA”循环是执行这一工作的常用方法,与“失效模式与影响分析”即“FMEA”一样用于预测可能的问题。最后,制定详细的实施计划,以指导如何解决现有的流程问题。
控制:
DMAIC 方法的最后一步可以帮助您验证解决方案并确保取得持续成功。在控制阶段,您的团队制定(您猜对了)控制计划,以便不断重新评估已实施流程发生变化所产生的影响。您还应该制定应对计划,以便在性能再次开始下降时采取行动。能够回顾您是如何进行改进的,以及您提出了哪些宝贵的解决方案。在这些时候,对改进流程编制适当的文档并执行版本控制至关重要。
需要注意的是,如果您对 DMAIC 已有所耳闻,那么您可能听说过一个不同的初始步骤,称为“识别”阶段。它的语义区别很小;两者本质上是相同的。
DMAIC 的优点是什么?
在工业领域,采用六西格玛和 DMAIC 有助于推动精益生产方法,以便消除浪费、缺陷和过度生产。(有趣的是,六西格玛这个名字源自所使用的统计模型:在统计学中,标准差也被称为 “西格玛” 或 σ。)
制造商发现,他们的平均和可接受质量极限之间的标准差越大,越不可能超过这些极限。因此,六西格玛或六个标准差成为定义生产极限、减少缺陷数和改进流程的黄金标准。
这种识别和解决问题根本原因的统计方法以及 Kaizen 等其他方法,在 20 世纪 90 年代和 21 世纪初对于推动制造业的改进至关重要。
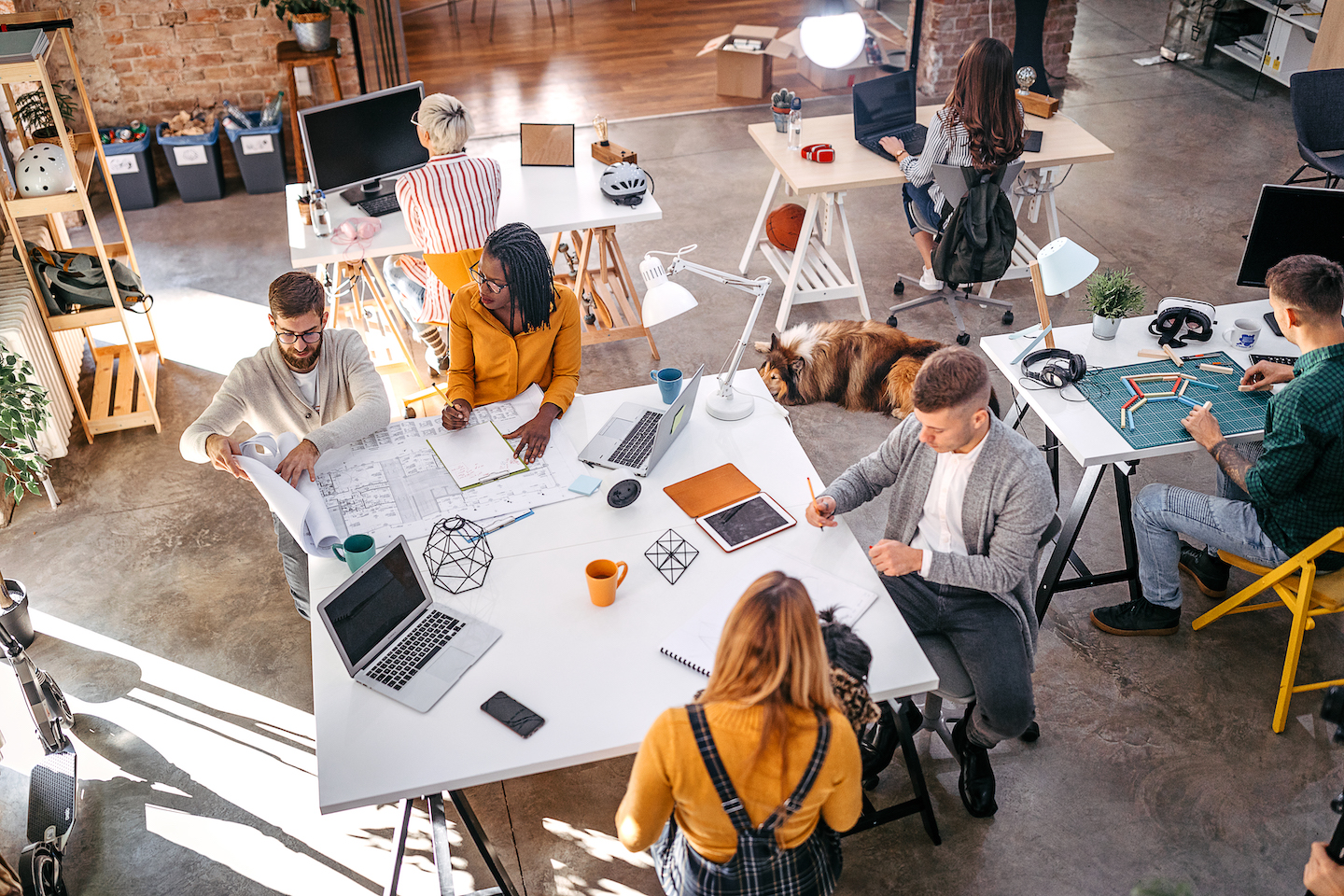
无论您是否在制造业工作,DMAIC 的核心优点是它非常严谨。使用新流程解决问题的实验通常最终无法得出有关变化内容的明确答案。通过使用 DMAIC,您可以更好地使用数据评估和测量进度。
DMAIC 的标准化五步框架让每个人都能了解流程的每个阶段。通过编制文档来汇总所有决策和所取得的进展,您可以无缝地逐步向前推动。而且,通过制定明确的流程,您还可以帮助指导团队实现其当前目标。
DMAIC 最受欢迎的是它具有迭代性和持续性:在流程的控制阶段,流程所有者必须继续监控优化的影响。如果已制定该数据监控计划,新流程数据自然就构成新测量阶段的基线。DMAIC 方法能够持续发现业务流程的问题或对其产生的影响,以及找到一种直接针对这些问题的解决方法。
何时应该使用 DMAIC?
团队需要协调并花费一些时间来了解 DMAIC。作为经理,值得一问的是,"哪个流程或团队最能从 DMAIC 中受益?"
需要记住,它并不一定是解决您的问题、行业和组织文化的正确选择。如果可以确定某个流程问题,并且有可靠数据支持的前瞻性简单解决方案,则意味着可能不需要完整的 DMAIC 流程。
当流程问题更复杂或风险更高时,例如当您承受不起性能下降时,DMAIC 可能是一种明智的策略。即使所需预算比预想的更多,但如果实施得当,此流程应该会产生不错的成果。
试用 DMAIC 修复问题
尽管第一次尝试 DMAIC 项目可能令人生畏,尤其是在您的组织遇到重大问题时,但这是一种解决问题的学术方法—类似于科学过程。您应该通过专注于发现、迭代和渐进式改进,为团队找到最佳实践,从而进一步为您的公司带来可观的成功。